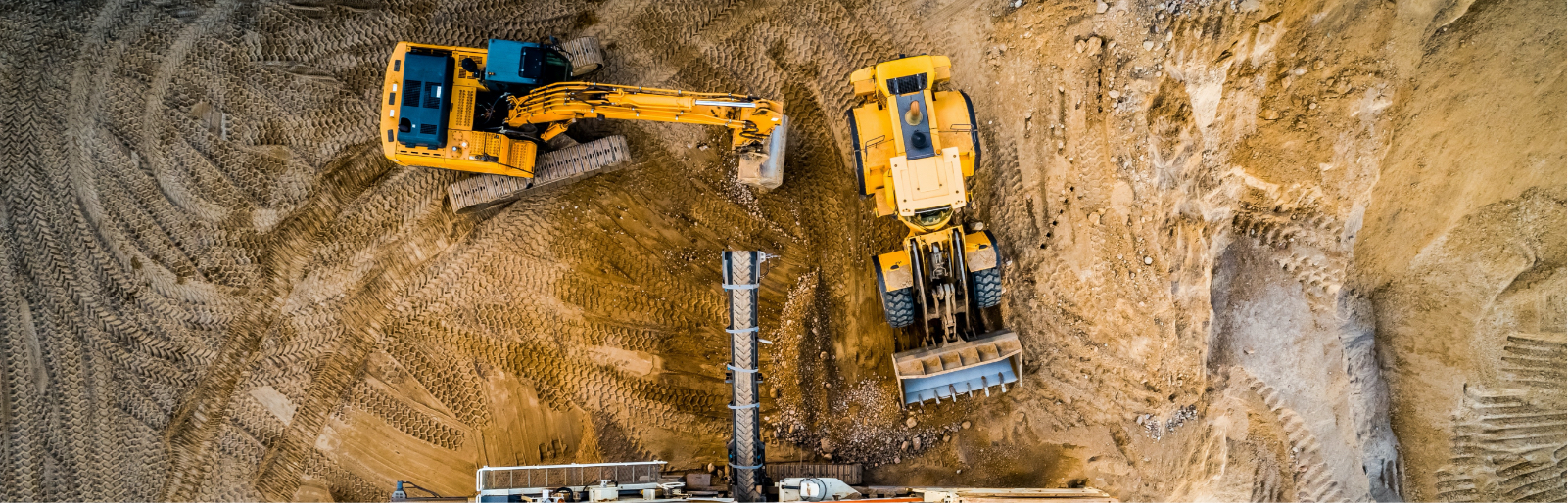
The Newsroom
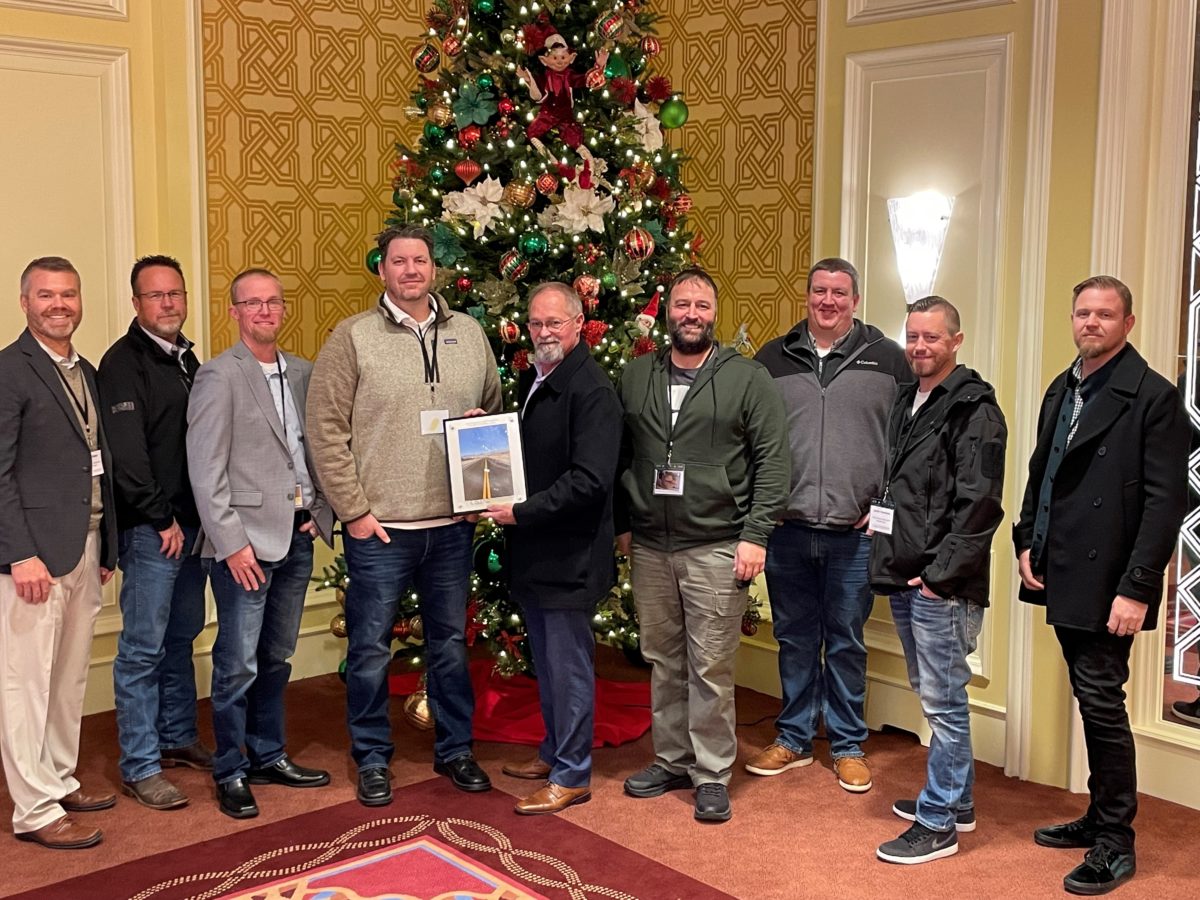
December 13, 2022
Staker Parson Materials & Construction Project wins Utah Construction & Design Award
View Article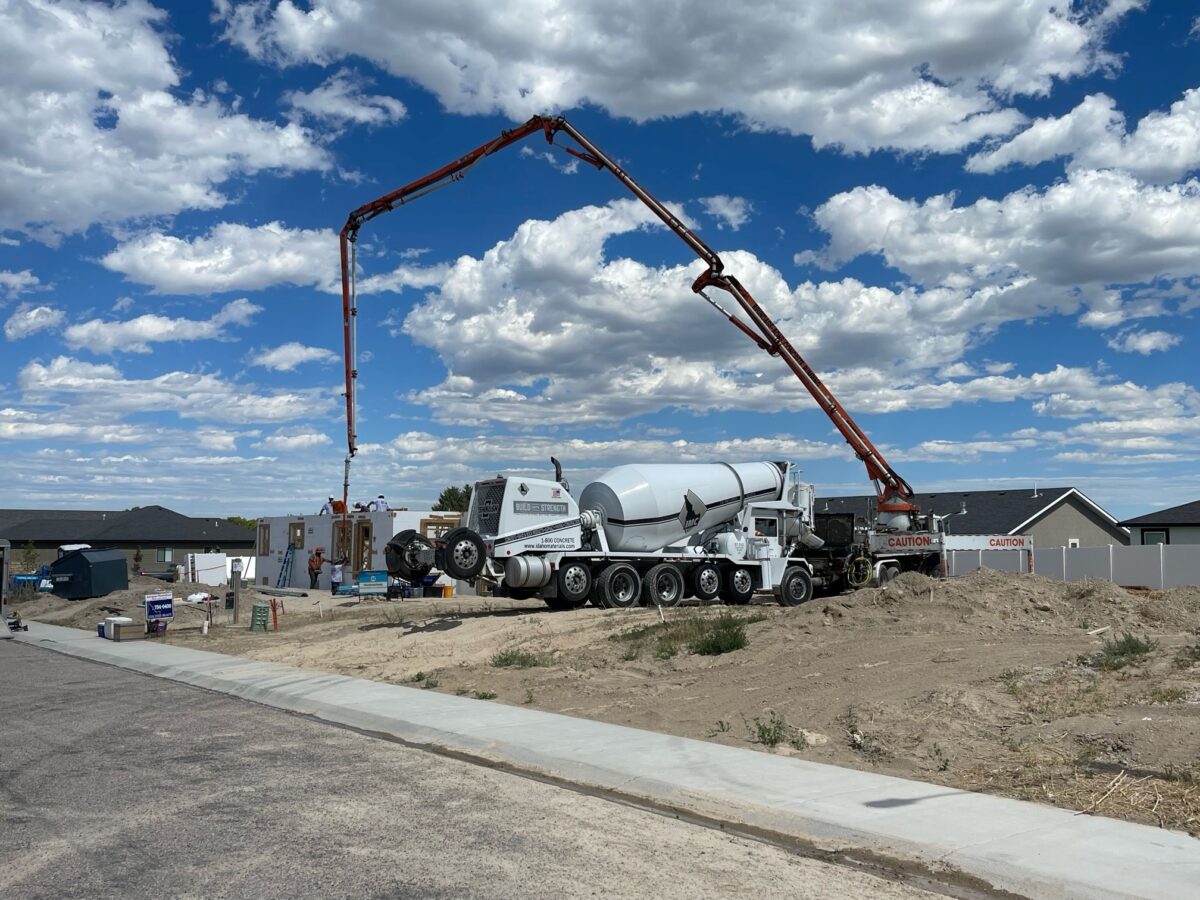
September 8, 2023
Idaho Materials and Construction involved in Habitat for Humanity Home Project
View Article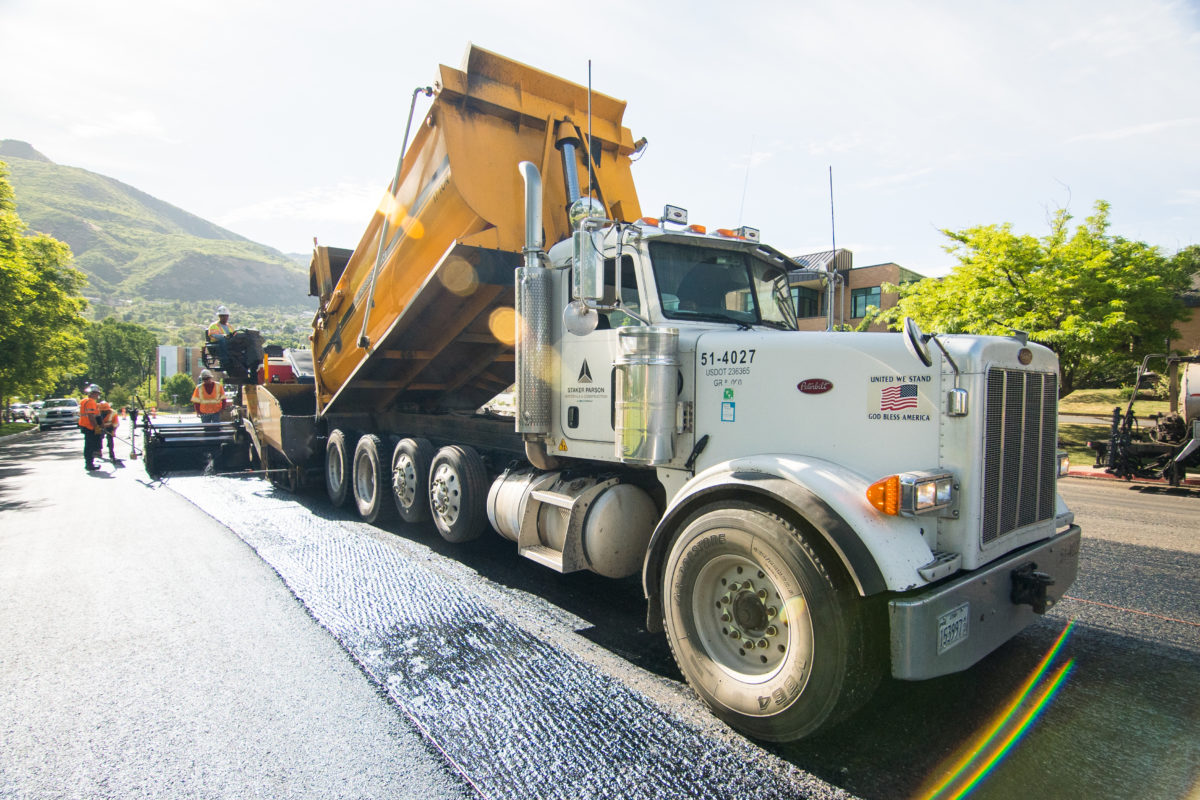
October 6, 2022
Staker Parson Awarded Business of the Year by Davis Chamber of Commerce
View Article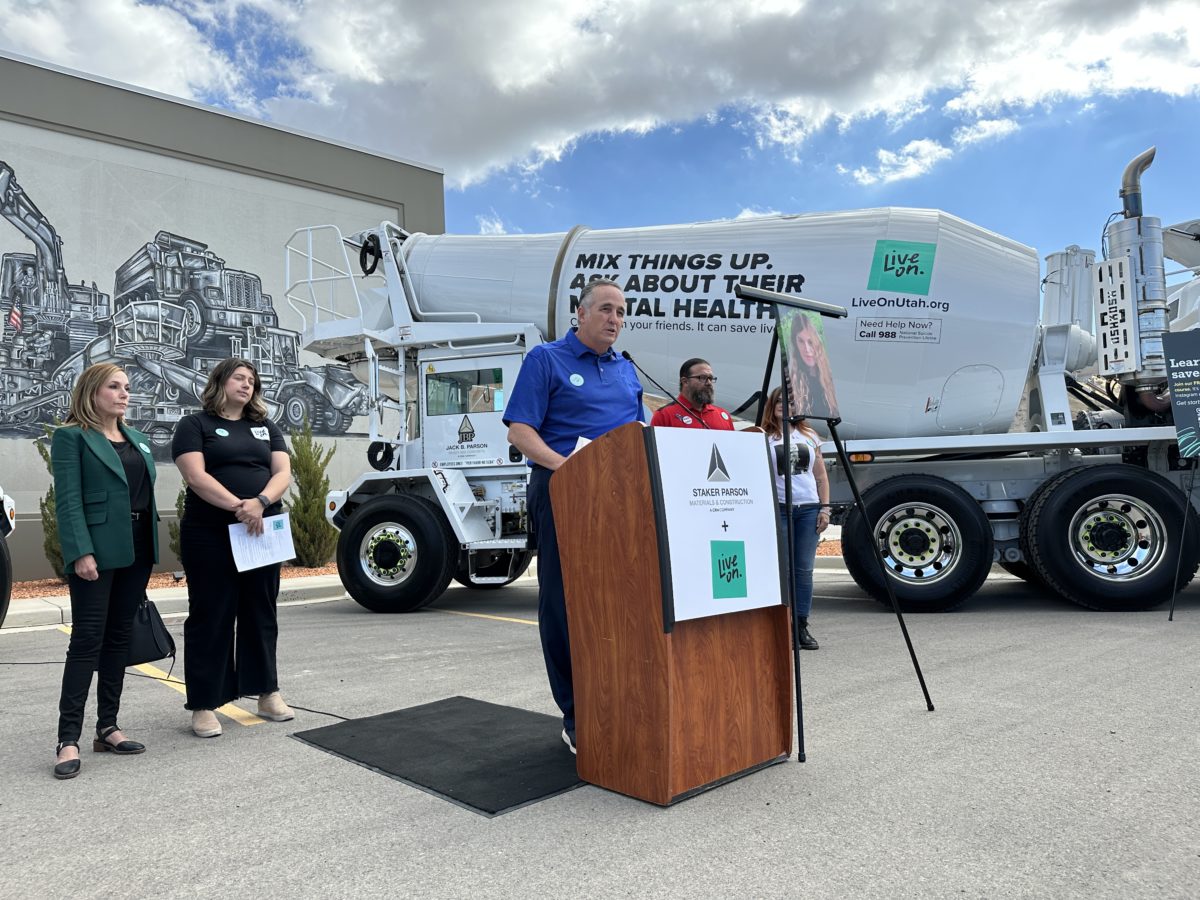
September 26, 2022
Staker Parson and Live On Utah Partner for Suicide Prevention Awareness
View Article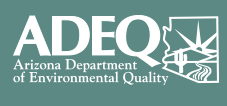